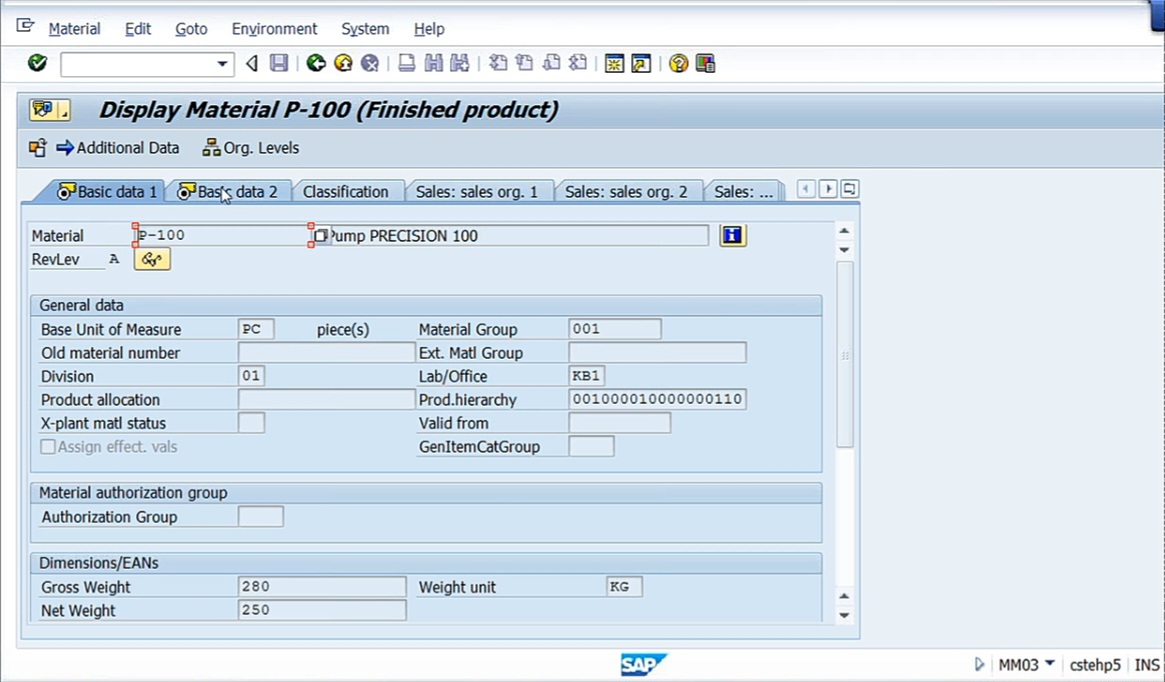
FI-MM Integration 2
Integration between FI and MM, so I told you that different types of materials will be there material type, ROH, etc. Each material type will be again given a valuation class. Valuation class is a component which is going to make the system to post the accounting entries through this valuation class and it will identify the GL account. For the purpose of posting it to GL account, valuation class plays a major role in posting the amounts to the respective GL account. Because by taking the reference number of the validation class, we are going to assign GL account. Anyway, that we’ll see. So in the accounting view of the material master, amongst other values, we have valuation class field.
Thank you for reading this post, don't forget to subscribe!So in case of material, if you want to procure material, you need to have a material Master record. Just like for GL account, we have GL master, Customer -customer master, Vendor -vendor master, like that, material -material master we have. So Material Master has various views right from the basic view of purchasing views, production, sales and distribution, accounting, controlling views, etc. You know, out of all the master records, material master is the highest, means having highest number of fields in SAP. More than 1125, I think. More than 1125 fields are there in the material master record. So that material master record will be accessed by material people, that is MM consultants, SD consultants, FI consultants, CO consultants, PP consultants, quality consultants. So for all these people, each module we have around 1 or 2 tabs. For FI and CO, we have 4 tabs completely reserved for this. So it’s one of the biggest material master records of the SAP. Views means each view we have in a tab. In accounting view of the material master, amongst other values, we have valuation class field. This valuation class is the vital link which ensures that accounting documents are posted automatically. So I’ll show you how it works, and also I have shown you how a material master looks like. It is display. MM03. Say, one material, P-100.
So like this sales text, purchasing, so many tabs are there. Accounting 1, accounting 2, costing 1, costing 2. All these things belong to financial accounting.
Plant 1000, storage location, 0001.
So these are the fields in material master. So basic data, basic data 2. MRP means material requirement planning 1, 2, 3. Accounting 1, Accounting 2, Costing 1, Costing 2. So here this is the valuation class. So valuation class is a vital link which ensures that accounting documents are posted automatically. You can go to the transaction code MM03. Put any material number. That’s what we have done. The combination of this value class plus movement type. So yesterday, we were discussing with the movement type also. Movement type is nothing but goods receipt is defined with 101. Goods issued to production order means you imagine that this is for production, that is raw material consumption. So goods issued to the production is defined with 261. Scrapping of goods is defined with movement type 551. Goods delivered to the customer, 601. Initial upload of stock, defined with moment type 561. Nothing but opening balances, entry of the opening balances. SAP helps us to have different GL accounts for various movements for the same material by linking this movement type to the transaction key. So here I’ll give you a small example.
When you receive the material, it may be received from vendor or received as upload of opening balances. Similarly, issue. You are issuing raw material. When you are issuing, you may be issuing for production that is consumption of raw material and when you are issuing sample quantity, say, for example, as a sample you are issuing to somebody outside or maybe for anything. And, scrapping mean there’s a loss. So, say, for example, one material, we have procured it, but because of the time lag, we could not use the material, so it got expired, because especially this kind of material means that, for example, chemicals, etc, which are used in the factories. So if you are not going to use within a particular time, it will get expired. So that kind of things can be scrapped. Even for scrapping, you are going to incur some expenditure. You cannot scrap just like that. You cannot pour in the chemical in the outlet. You have to properly dispose it off, as per the norms. Even sometimes that may cost. Also quality testing, maybe we may be issuing the material for quality testing. Like that, system should understand what is the purpose of issue of material. Because in every case, if you observe, in the production, material is going out. Sample, material is going out. Scrapping, material is going out. Quality testing, material is going out. In each and every activity, the ultimate result is that material is going out. But while going out, every activity of going out has got a significance. Here, if you’re issuing for production, yes, it is going to be consumed. So that should be booked to consumption account, account to which we have to debit our credit. Next, sample quantity. Sample for the quality department. So for sample expenses, there is also booked as expenses. Scrapping is a loss, this should go to loss or scrapping of raw material account. So ultimately, there is a loss. So the purpose of this issue is different in each case. We need to understand that. Just like in case of special GL indicator, when you are paying advance to the vendor, we use A. So A is nothing but advance. So system, how it knows whether we have received advance or regular payment, that is only based on the special GL indicator, we use it if it’s an Advance. Similarly here also, we are going to use different movement type for the different issues.
So here, in accounting, 7920, this is nothing but the valuation class.
Here, there are two (2) ways to go to the integration. The T code is OBYC. Straightaway, we can go ahead, but I want to take you through the path. General Ledger Accounting, Periodic Processing, Integration, Materials Management, Define Accounts for Materials Management.
Here, the t code is OBYC. So here in this note, another path is given.
You can go through that path also. Let me go through here. So SAP helps us to have different accounts for various movements for the same material by linking this movement type to the transaction key. This is what I told you. There is the valuation class and raw material may be used for different purposes. And, I told you in different cases that there are account keys or transaction keys. Now those things will come into picture again.
So here, these are all transaction keys. Before we go for the looking of all these configuration configurations, let’s see the GL accounts. What are the entries to be posted when raw material is received. Generally what we do, inventory of raw material account return to vendor account. But if you are going through the material master, that is materials management system, the accounting entry as soon as you receive the material, they will enter into the MIGO, the T code called MIGO, and, inventory of raw material account return to GR/IR clearing account. So what is the GR/IR clearing account? This is one temporary clearing account. It will get nullified once the invoice is verified. So when invoice is verified, GR/IR cleaning account is debited and vendor account is credited. Ultimately, if you observe, inventory of raw material account return to vendor account. So this will get nullified because there will be a time gap between the time we have received the material and invoice is received. And once you receive the material, unless you get the commercial invoice or something, we cannot credit the vendor. And it has to be as a process of verification. one person will be receiving the material, another person will be using the invoice verification process.
So now, let us now understand the transactions for accounting integration. Goods receipt of material against purchase order. So PO, purchase order. So when goods are received, movement type for goods receipt against the purchase order is 101. Goods received is defined with movement type 101. Nothing but goods received from vendor. The accounting entry posted as follows: Inventory of raw material account debit, GR/IR (Goods Receipt/Invoice Receipt) account is credit. The GR/IR is a provision account in SAP. And the configuration to be done for this is OBYC. So once you go to OBYC, you’ll go to the screen. You need to update BSX. Let’s see here.
So OBYC and so our company code is for DRL, I’m going to do. Now the thing is, since we do not have settings, we are not going to configure the integration part because unless you have all the objects of materials management, we cannot create. So that’s why I want to show you the integration configuration that has already been done for the company code 1000, and for that INT is the chart of accounts, international chart of accounts. Now this kind of screen, we have seen in case of sales tax. For integration with the sales tax, we have seen this kind of table. So here, anyhow, for each and every type of transaction, we have to use one transaction key, and by using that, you have to assign the GL account. See here, GBB. See. As you have seen, the above second column contains all the transaction keys wherein you need to stick the GL accounts. So here, this is the accounting key or transaction key. You need to update the BSX transaction key with the GL code inventory of raw material account.
Say here, BSX. What is BSX? Inventory posting. What type of accounting entry I need, my requirement is that when raw material is received, inventory of raw material account return to GR/IR clearing account. So in order to get this accounting entry, what you need to do, first of all, double click on inventory posting. Chart of accounts, I’m going to take INT chart of accounts. So in case of INT chart of account, see here valuation class 3000.
So valuation class 3000 means raw material, 3000 raw material 1, raw material 2, like that. So against this, valuation modified, this is nothing but the plant, the plant in which this configuration is being done. Even if you don’t enter this, system will not throw any error, there’s not a problem. But valuation class, you need to see. If it is a valuation class 3000, then you need to assign it to the respective GL account. So if it’s a valuation class 3000, 3000 represents raw material. This is what I told you.
Here, of course, 7920 is given, 7920 is for finished goods. So I told you, say 3000 valuation class for raw material, for finished goods 7920, semi finished goods 7900, operating supplies, spare parts. So these are the valuation classes we have to use. Now, here BSX is the transaction key for international chart of accounts I’m going to define. I’m telling to the system, in case if it is a raw material, post to this account. So let me check what is this account for company code 1000. We are just looking at the configuration that has been done for 1000. Go to FS00
See, 3 lakhs. I want to show you what is the GL account for 1000 company code.
Inventory of raw material 1.
So here, if the valuation class is 3000, see here list of valuation classes are there. So this 3000 raw material, 3030 operating supplies, 3040 spare parts. So like that different valuation classes are given. For each valuation class, we need to assign a respective GL account. So similarly, 7920.
So 7 lakh 92,000. See, finished quotes inventory. All are inventory only. Similarly, in fact, somebody has disturbed with this setting because it will have more and more accounting entries for INT BSX transaction. Even 7920 is for finished goods. So, right, if it’s a raw material, it should go to this account. If it’s a finished goods, finished goods. And here, SAP Fellow, he synchronizes the GL accounts. 7920 means here also he is using 7 lakhs 92,000. Here, what is 3100? Let me check this.
See trading goods. 310,000 trading goods. 7,920 finished goods. So, like that depending upon the valuation class, if you know the valuation class, you can assign the GL account. So without knowing this, you cannot do. That’s why even FIMM integration, we need to carefully go through.
Next, so you need to update BSX transaction key with GL code inventory of raw material account. So for INT chart of accounts, BSX is the transaction key, 3000 is the raw material for us. And if it’s a raw material, how to post to this account. There is the sequence. You need to update BSX. Updating BSX means, see, simply double click on BSX. So for this key, we have to update it.
Double click and BSX for all these GL accounts I need to assign.
So you need to update BSX transaction key with GL code inventory of raw material account. Double click BSX and select valuation modifier and valuation class. Valuation modifier is nothing but should be selected if valuation grouping code is active in materials management module, and if separate GL codes are desired plant wise. So valuation modifier is nothing but for each plant, we need to represent one valuation modifier. And, as per the SAP system, separate GL codes are designed plant wise. Even if it is not required currently, still it is a better option to select. So validation modifier, it doesn’t mean that we have to use validation modifier. Even without that, we can go ahead. Valuation modifier, valuation class, both we need to check. So in such case, what happens you know, for the GR/IR account, you need to update WRX. So what is the accounting entry I require? First of all, my accounting entry is inventory account return to GR/IR clearing account. So this GR/IR clearing account is a temporary provision account. And which key we need to update for inventory of raw material, BSX I told you, for GR/IR clearing account, we need to update WRX. So what is that? So what I do here.
Here, GR/IR clearing account. To get the GR/IR account credit or debit, you have to double click here and assign the respective GL account here.
See, even this also somebody has spoiled. We should not use valuation class here because valuation class doesn’t have any meaning here. The reason being, GR/IR clearing account, so that will not have any material here. But anyhow so this is the GR/IR clearing account. We should not disrupt the standard ones, people doesn’t know.
So this is GR/IR cleaning account. So for GR/IR account, you need to update WRX transaction key. So here, directly on WRX and enter the GL account, so that system automatically will post first stage raw material consumption account, raw material account return to GR/IR clearing account. So this entry, if we want, in weight of raw material account return to GR/IR clearing account, if we want this entry, we need to do this configuration.
So here, one more thing you may have a doubt. How how about the 2nd entry? 2nd entry, anyway, GR/IR clearing account, we have given WRX as the account key. BSX is the account key for the inventory of raw material. Means, there’s inventory posting, we use the BSX key.
If you observe here, so for international chart of accounts for BSX transaction key, these are the GL accounts we are going to post. As an FICO consultant, you need to understand what is valuation class, valuation modifier, and other things, then we need to give this GL account. That’s all, not more than that. The second entry, you need not direct confirmation because GR/IR is already there, and vendor account is not a part of integration. So we are going to give the vendor number. System automatically picks up that vendor account if you give the vendor number. So for that purpose, we need to update WRX. That’s what it is being told here.
Okay, second entry, When raw material is issued to the production order means to the production, movement type to be used is 261. Of course, that will be taken care by MM consultant, and the accounting entries as follows: Raw material consumption account debit, Inventory of raw material account is credit. So three, when when raw material is issued to production, the accounting entry will be raw material consumption account return to inventory of raw material. So this is the accounting entry. So raw material account is debit and inventory of raw material is credit. Because raw material consumption account should be debited because there is booking to consumption. So for that purpose, we need to update transaction key GBB. What is that GBB? This is also one of the transaction keys we use. For updating, opening balances, etc, we are using BSX. Let’s see GBB. There’s a huge one.
This is GBB. Offsetting entry for the invoice posting. What is meant by offsetting entry? Balancing entry, means, what is the original entry? Original entry is nothing but procurement of raw material. Raw material account return to vendor account. That is, of course, split into the 2 accounts like GR/IR clearing account, etc. So here, for raw material consumption, this is bit complicated. Just to understand, here, the transaction key GBB need to be updated. For raw material consumption account, GBB. See, here we have already done with BSX. Now for offsetting entries, GBB key need to be updated. Double click on GBB, and we need to assign the GL accounts here as FICO consultant. But in order to assign these GL accounts, you need to understand what is this. So the transaction key GBB need to be updated, and GBB key is used for various offsetting postings. Within GBB transaction, there are various account grouping, that is general modification. What does it mean? Within GBB, various offsetting posting entries within GBB transaction, there are various account grouping. That means see, here I told you for configuration for issuing of raw material, we have to use GBB transaction key. For that GBB there’s nothing but offsetting entry, what is the first entry? First entry is getting of the raw material, second entry to adjust that, issue of raw materials is nothing but offsetting entry. So that’s why it’s says that GBB transaction key need to be updated. GBB key is used for the various offsetting entries. Within GBB transaction there are various account groupings (general modifications), that means when I told you if it is a production, it should go to consumption, if it is a sample, go to sampling, scrapping, scrapping. How system is going to understand when a raw material is being issued whether it is going to the raw material consumption or it is going to the sample or we’re going to get the scrapping loss, so all those things we need to understand. So we call this as general modification.
What is general modification I’ll tell you. You know valuation class already, so valuation class is nothing but it will identify the type of material whether it’s raw material or finished goods or semi finished goods, whatever it may be. So, what is general modification? So I’ll show you general modification for 00011 company code. In this case you need to update general modification VBR with the raw material consumption account. So in order to identify the purpose of issue, I told you, there are three purposes I’ve given, in each case material is going out. But what feature is going to identify the purpose here? This is the general modification key. Is it production, consumption, then we have to tell to the system VBR, VBR with the raw material consumption account.
So here, valuation modifier, general modifier, and this is the valuation class. If this is the combination, give the GL account 4 lakhs.